⊙ 언박스드 프로세스, ▲자동화에 의한 생산성 향상 ▲제조 시간 단축 ▲공장 콤팩트화 가능
⊙ 토요타, SSC(Simple, Slim, Compact) 통해 고객 변화에 유연하게 대응 추구
⊙ 사토 고지 신임 토요타 사장도 전기차 공장 공정 수를 1/2로 줄이겠다고 발표
⊙ 생산성 낮은 공장은, 공장과 연구소, 본사 간에 벽 높아
⊙ 자동차 산업의 대전환기, 현대자동차의 공장 혁신은?
朴正圭
1968년생. 한양대 기계공학과 졸업, 한국과학기술원 기계공학과 석사, 일본 교토대 정밀공학과 박사 / 기아자동차 중앙기술연구소 연구원, 日 교토대 정밀공학과 조교수, LG전자 생산기술원, 현대자동차 자동차산업연구소·해외공장지원실 근무. 現 한양대 미래자동차공학과 겸임교수, 글렌데일 홀딩스 부대표 / 번역서 《실천 모듈러 설계》 《도요타 제품개발의 비밀》 《모노즈쿠리》
⊙ 토요타, SSC(Simple, Slim, Compact) 통해 고객 변화에 유연하게 대응 추구
⊙ 사토 고지 신임 토요타 사장도 전기차 공장 공정 수를 1/2로 줄이겠다고 발표
⊙ 생산성 낮은 공장은, 공장과 연구소, 본사 간에 벽 높아
⊙ 자동차 산업의 대전환기, 현대자동차의 공장 혁신은?
朴正圭
1968년생. 한양대 기계공학과 졸업, 한국과학기술원 기계공학과 석사, 일본 교토대 정밀공학과 박사 / 기아자동차 중앙기술연구소 연구원, 日 교토대 정밀공학과 조교수, LG전자 생산기술원, 현대자동차 자동차산업연구소·해외공장지원실 근무. 現 한양대 미래자동차공학과 겸임교수, 글렌데일 홀딩스 부대표 / 번역서 《실천 모듈러 설계》 《도요타 제품개발의 비밀》 《모노즈쿠리》
- 일론 머스크. 테슬라는 3월 1일 ‘언박스드 프로세스’라는 새로운 자동차 생산방식 도입을 선언했다. 사진=로이터/뉴스1
자동차 산업의 변화를 흔히 CASE라고 부른다. 이것은 2017년 1월 CES에서 메르세데스-벤츠가 자사(自社)의 미래 전략을 발표하면서 사용한 용어로, 커넥티드(Connected), 자율주행(Autonomous), 공유 및 서비스(Shared & Service), 전기 구동(Electric Drive)을 의미한다.
CASE라는 키워드를 곰곰이 살펴보면 기존 자동차 산업을 부정하는 용어로 이해된다. 즉 독립공간인 차에 연결성을 부여하고, 운전의 즐거움을 강조하는 기존 차량과 달리 자율주행을 추구하고, 또 차량을 소유하지 않고 공유하며, 엔진이 아닌 배터리와 모터로 움직이는 자동차를 의미하기 때문이다. 많은 메이커들은 이처럼 지난 100년간의 자동차 산업의 역사를 부정하고 있다.
테슬라의 언박스드 프로세스
테슬라는 3월 1일 인베스터데이(Investor day)에서 또다시 자동차 생산 방식에 대해 부정했다. 언박스드 프로세스(Unboxed Process)가 바로 그것이다. 지금까지 자동차 메이커는 차량의 골격에 해당하는 차체(Body)를 먼저 완성시키고 난 뒤에 차체에 부품을 하나씩 장착하면서 차량을 완성했다. 하지만 테슬라는 차량을 6개의 빅 모듈(Big Module)의 조립만으로 완성하겠다고 발표했다. 이 방법을 통해 전기차의 제조 코스트를 2분의 1로 줄이겠다고까지 했다.
물론 이것을 실현하기 위해서는 해결해야 할 기술적 난제가 많을 것이다. 하지만 일론 머스크와 테슬라가 생각하는 자동차의 설계와 생산 철학을 살펴볼 필요는 있다. 테슬라의 이번 발표를 그냥 넘기기에는 제조업이 생산시스템에서 차지하는 비중이 크기 때문이다. 생산은 개발과 함께 제조업을 이루는 양대 축에 해당한다. 현대자동차의 경우, 경기도 화성의 남양연구소에서 차량을 개발하고, 울산 공장에서 차량을 생산한다. 물론 서울 양재동의 본사에서도 다양한 업무를 처리하지만, 제조업의 본질, 그리고 현대자동차를 구성하는 인력의 분포를 보더라도 연구소와 공장을 2개의 축으로 볼 수 있다.
테슬라는 사물을 제로 상태에서 바라보면서 근본적인 문제 해결을 추구하는 기업이다. 그동안 테슬라의 일론 머스크는 기존 자동차 생산시스템에 대한 지속적인 의문을 제기해왔다. 이번 기회를 통해 제조업에서 생산시스템의 주요 이슈와 변화 방향에 대해 살펴볼 필요가 있다.
먼저 테슬라가 발표한 언박스드 프로세스가 무엇인지 설명하겠다. 그리고 기존 메이커가 개선해온 생산 방식의 특징과 전기차를 생산하는 방식에 대해 살펴보고, 한국 제조 기업이 처한 상황과 나아가야 할 방향에 대해 논의하는 기회를 가지려고 한다.
기존 자동차 제작 공정
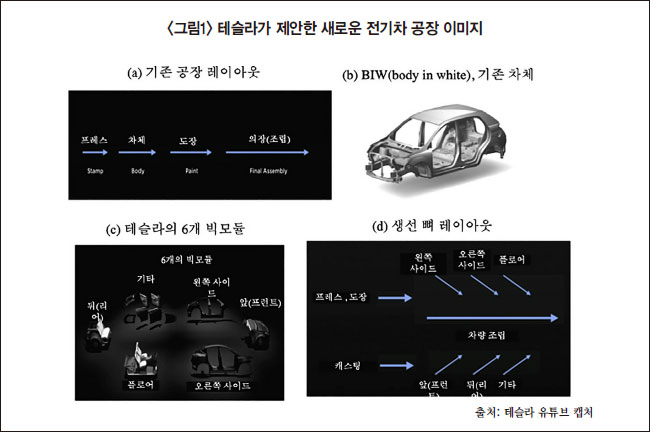
먼저 기존 자동차 공장의 생산 방식을 살펴보자. 기존 자동차 공장은 프레스, 차체, 도장, 의장(조립) 공장의 순서로 구성되어 있다.
연구소에서 제품을 설계하면 설계 정보를 금형(金型)이란 큰 틀에 새겨 넣는다. 그리고 금형을 프레스 기계에 상하로 장착하고 철판을 금형 사이에 두고 세게 누른다. 그러면 철판은 설계된 형상으로 변형된다. 이후 성형(成型)된 부품을 차체 공장에서 용접하여 3차원 형상의 차체를 만든다. 자동차 회사에서는 이것을 BIW(Body in White) 또는 화이트 보디(White body)라고 한다. 아직 페인팅이 되기 전의 상태이기에 붙여진 이름이다. 차량의 골격을 정확하게 용접하지 않으면 내구 성능, 충돌 성능 등이 나빠지기에 상당히 주의를 기울인다.
이후 이 BIW를 도장공장에서 페인팅하고, 의장(조립) 공장에서 도어를 제거한 뒤에 차량 내부에 부품을 장착한다. 그러고 차량 하부에 차의 기본 성능을 좌우하는 섀시(chassis) 부품(예를 들면, 엔진, 서스펜션 등)을 장착한다. 마지막으로 도어를 다시 장착하여 차량을 완성한다. 물론, 프레스, 차체, 도장, 의장 공장 사이에 재고(在庫) 창고가 있지만, 하나의 선(라인)이 순차적으로 연결된 형태라고 생각해도 큰 무리가 없다.(〈그림1〉 (a), (b) 참조)
언박스드 프로세스, 자동화 용이
기존 자동차 메이커는 BIW(또는 화이트 보디)라는 차체의 형상을 먼저 만들고 난 뒤에 차량 내부의 부품을 조립한다. 이 경우 차량 내부에 조립 설비가 들어가고 나오기가 어려워 일정 비율 이상 자동화가 어렵다. 그래서 어쩔 수 없이 사람이 계속 차 밖에서 부품을 잡아 차 안으로 들어가서 부품을 조립한다. 당연히 생산성이 떨어진다.
테슬라의 새로운 공정은 3차원 폐공간(closed space), 즉 BIW를 만들지 않겠다는 발상에서 출발한다. 테슬라는 차량을 크게 6개 모듈(차량 앞, 중간, 뒤 부분과 왼쪽·오른쪽 사이드, 기타 부분)로 나누어서 페인팅과 조립을 완료하고 난 뒤에 마지막 단계에서 6개의 빅 모듈을 하나로 합쳐 한 대의 차를 만들고자 한다. 그리고 자동차 공장의 레이아웃(layout)도 기존의 1자 라인에서 생선뼈와 같은 형태의 레이아웃으로 완전히 변화시킬 에정이다.(〈그림1〉 (c), (d) 참조)
직선으로 연결된 기존 자동차 공장의 레이아웃과 테슬라가 제안한 생선뼈 모양의 레이아웃 간의 차이를 살펴보자.
언박스드 프로세스의 장점은 첫째, 자동화에 의한 생산성 향상이다. 앞서 말한 것처럼 BIW는 박스(box) 형태의 폐공간 때문에 자동화가 힘들다. 현재 의장 공장의 자동화율은 15% 수준으로 알려져 있다. 하지만 테슬라의 언박스드 프로세스는 오픈된 공간에서 모듈 단위로 조립하기 때문에 자동화가 용이하다. 그리고 작업자의 접근성이 높아져 생산성을 올릴 수 있다.
대폭적인 비용 절감 가능

둘째, 차량을 제작하는 데 소요되는 시간(리드타임)을 극적으로 단축시킬 수 있다. 기존 공장은 4개의 공장을 직렬로 배치하여 공정이 순차적으로 진행되기 때문에 일정 정도 시간이 걸린다. 하지만 언박스드 프로세스는 6개의 빅 모듈이 동시 병행으로 조립하기 때문에 한 대의 차를 제작하는 데 소요되는 시간(리드타임)을 극적으로 단축시킬 수 있다.(〈그림2〉 참조)
셋째, 공장을 콤팩트화할 수 있다. ‘생선뼈’처럼 생긴 레이아웃은 척추(backbone)에 해당하는 메인 라인과 6개의 서브 라인으로 구성되어 있다. 이것은 현재 생산 라인보다 훨씬 더 콤팩트한 생산 라인을 만들 수 있다. 테슬라는 생산 라인의 설치 면적을 40% 이상 줄일 수 있다고 한다. 생산 라인의 소형화는 공장을 신·증설할 때 위력을 발휘한다. 기존 생산 방식보다 초기 투자 비용을 절감할 수 있을 뿐 아니라 공사 기간도 줄일 수 있다. 즉 보다 저렴한 비용으로 빠르게 전기차 양산 공장을 만들 수 있다.
테슬라는 언박스드 프로세스를 도입하여 대폭적인 비용 절감을 노리고 있다. 현재 고객은 테슬라가 만들고 있는 ‘모델3’의 절반 가격(2만5000달러)인 전기차를 기대하고 있다. 테슬라는 2030년에 2000만 대의 차량을 생산하겠다고 발표한 적이 있다. 이 목표를 달성하기 위해서는 대중적인 가격의 차가 필수적이며 언박스드 프로세스가 해결안이 될 수 있다. 6개 빅 모듈의 조립만으로 하나의 차량을 만들기 위해서는 차량 설계를 근본부터 다시 변경해야 한다. 그래서 테슬라는 설계와 생산 기술 부문이 서로 같은 팀에서 일하고 있다. 아마도 언박스드 프로세스에 가장 적합한 형태로 차량을 새롭게 개발할 것이다.
테슬라, 공장 개념의 전환
여기서 관심 있게 보아야 할 것이 하나 더 있다. 테슬라는 그동안 전개해온 ‘기가 팩토리(giga factory)’라는 공장 개념을 가지고 있었다. 그런데 갑자기 언박스드 프로세스라는 것을 들고나왔다는 점이다.
기가 팩토리는 테슬라가 GM과 토요타로부터 인수한 캘리포니아의 프리몬트(Fremont) 공장에 이어 본격적으로 생산량 확대를 위해 만든 표준 공장에 대한 개념이다. 중국 상하이(2019년 10월), 독일 베를린(2022년 3월)에 이어 미국 텍사스(2022년 4월)에서도 가동을 시작했다. 테슬라는 자사 공장에 ‘기가(giga)’라는 이름을 붙일 만큼 공장 규모가 크다는 것을 자랑했다. 텍사스 공장의 길이는 1166m로, 현존하는 세계 최고 높이의 건축물인 163층의 부르즈 할리파 빌딩의 높이 829m보다 길다. 면적은 약 40만㎡에 달한다. 이것은 100년 전 헨리 포드가 만든 공장과 닮았다.
사실, 테슬라의 거대한 공장 규모는 자동차 메이커가 글로벌 톱 메이커로 올라서는 과정에서 거쳐 간 과정과 유사하다. 헨리 포드가 1928년에 완공한 리버루즈 공장은 자동차 공장 내에 제철소까지 만들었다. 일본의 토요타가 1950년대 말, 1960년대 중반에 건설한 모토마치 공장과 다카오카 공장 또한 당시에는 나름 거대한 공장이었다. VW(폴크스바겐)의 볼프스부르크 공장과 현대자동차의 울산 공장 또한 세계적인 규모의 공장이다. 현대자동차는 울산 공장 내에 5개의 완성차 공장과 함께, 엔진 공장, 변속기 공장과 수출 항구까지 갖추고 있다.
그런데 2023년 테슬라는 자신이 만든 ‘기가 팩토리’라는 공장 콘셉트를 바꾸고자 한다. 어쩌면 테슬라의 장점은 바로 이렇게 스스로 변신할 수 있다는 점일 것이다.
토요타의 SSC

테슬라가 언박스드 프로세스를 통해 공장을 콤팩트화하고 생산리드타임을 줄이겠다고 하지만, 사실 이것은 토요타 생산 방식의 핵심이다. 여기서 토요타 자동차 공장을 어떻게 개선해왔는지를 살펴보자.
토요타는 고객의 변화에 유연하게 대응할 수 있는 공장을 만들기를 원한다. 코스트 저감보다 업무 프로세스 개선이 더 중요하며 공장에서의 생산 흐름을 개선하면 자연스럽게 코스트는 저감될 것이라고 생각한다. 그래서 토요타가 제시한 공장 콘셉트는 심플(Simple), 슬림(Slim), 콤팩트(Compact)다. 줄여서 SSC라고 표현한다. 가능한 한 적은 투자비로 고정비를 줄이고 공장을 콤팩트하게 만들어 공장의 운영 비용을 줄이고자 한다. 좁은 공간에 로봇을 많이 설치하고, 노동 생산성을 올려 작업자의 수를 축소한다.
〈그림3〉(a)는 토요타 그룹의 경차 전문 메이커인 다이하츠가 이루어낸 성과물을 수치로 나타낸 것이다. 2004년 11월에 다이하츠는 규슈의 나카츠에 400억 엔을 투자하여 23만 대 규모의 공장을 건설하였다. 종업원 수는 약 2100명으로 경차와 소형차를 만든다. 이후 SSC 개념으로 공장을 혁신했다. 즉 2007년 11월에 만들어진 나카츠 제2공장은 235억 엔을 투자하여 제1공장의 절반의 면적에 동일한 생산 능력을 가지게 되었다. 종업원 수는 약 400명으로 제1공장의 19% 수준에 불과하다. 〈그림3〉(b)는 다이하츠의 나카츠 공장을 인공위성에서 찍은 사진이다. 왼쪽에 있는 나카츠 제1공장과 비교해 오른쪽의 제2공장이 동일한 생산 능력을 갖추고 있음에도 불구하고 얼마나 콤팩트하게 만들어졌는지 알 수가 있다.
생선뼈 형태의 공장 레이아웃
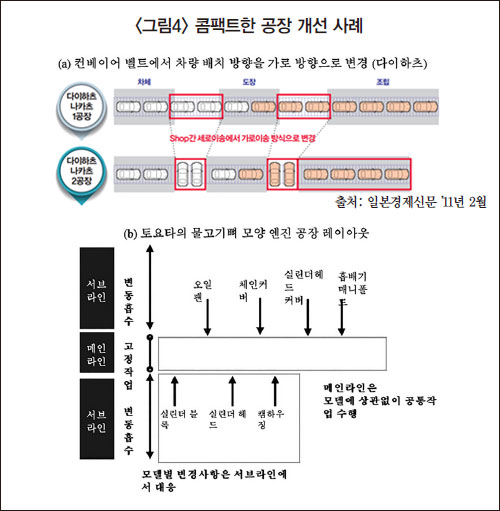
나카츠 제2공장에서 투자비를 줄인 예를 살펴보자. 먼저 차체를 용접하는 데 필요한 지그(Jig)를 없앴다. 보통 차체를 용접할 때에 차종마다 전용으로 설계한 지그가 용접하는 철판을 잡아준다. 하지만 많은 비용이 드는 지그 대신 로봇이 용접할 위치를 잡아 고정시킨 후에 용접한다. 이렇게 하여 지그 설치 비용을 줄였으며, 다양한 차종의 용접을 큰 비용의 증가 없이 용접할 수 있었다.
한편, 차체-도장-조립 공장 간 이송할 때 차량을 컨베이어 벨트상에 세로 방향으로 돌려서 이송하여 컨베이어 벨트 길이를 줄였다.(〈그림4〉(a) 참조) 이 외에 좁은 공간에 많은 로봇을 설치하였다. 나카츠 제1공장이 단위면적당 3.8대의 로봇이 설치되어 있는데, 나카츠 제2공장은 단위면적당 로봇이 11.4대가 설치되어 약 3배 정도로 로봇 설치 밀도를 올렸다.
그리고 테슬라가 언박스드 프로세스에서 발표한 생선뼈 형태의 공장 레이아웃도 사실 처음은 아니다. 〈그림4〉(b)는 토요타가 10년 전에 만든 엔진 공장의 레이아웃이다. 하나의 엔진 생산 라인에서 다양한 종류의 엔진을 만들기 위해 고안된 방식으로 엔진에 장착되는 각종 부품의 생산을 서브 라인으로 만들어두었다.
물론, 완성차 조립에 이런 레이아웃을 적용하겠다고 시도하는 것은 분명 테슬라가 처음이다. 테슬라와 토요타가 같이 생선뼈와 같은 레이아웃에 도달했지만, 공장을 통해 추구하는 목표는 서로 다르다. 테슬라는 철저하게 공장 자동화를 하고 싶어 하고, 토요타는 동일한 생산 라인에서 다양한 제품을 만들고 싶어 한다.
모듈형 vs 통합형
자동차 메이커는 저마다 창업 이후 성장하는 과정 속에서 시련을 겪고 또 문제를 해결해나갔다. 그러면서 그 경험이 조직의 노하우로 정착되었다. 결국 조직이 가지고 있는 경험이 지금과 같은 자동차 산업의 전환기에 서로 다른 의사 결정을 만들어낸다는 말이다. 또 제품과 일하는 방식에도 반영된다.
이런 의미에서 미국 실리콘 밸리에서 탄생한 테슬라는 확실히 모듈 관점이 강하다. 모듈이란 부품의 사이즈와 용도가 표준화되어 서로 교체하기 쉬운 설계 방식을 의미한다. 마치 레고처럼 인터페이스가 표준화된 부품으로 전체 제품을 만들겠다는 발상이다. 가령, 테슬라가 전기차에 사용한 배터리를 살펴보자. 테슬라는 18650 원통형 배터리(직경 28mm, 길이 65mm)를 사용하는데 이것은 과거 비디오 카메라용 배터리로 개발된 것이다. 테슬라는 18650 원통형 배터리 약 7000개를 서로 연결하여 전기차용 배터리로 사용한다. 모듈적인 제품 개발 방식이다. 테슬라가 새롭게 제안하는 자동차 조립 기술인 언박스드 프로세스는 차를 6개의 빅모듈의 조합으로 만든다는 것으로 모듈 생산의 끝판왕이라 할 수 있다.
이와 반대되는 설계 철학을 가지고 있는 회사가 있다. 바로 토요타이다. 토요타는 차량에 맞는 배터리가 필요하다고 생각한다. 이렇게 제품에 특화(特化)된 부품으로 개발된 제품을 통합형(Integrated) 제품이라고 한다. 일본의 제조 기업, 특히 토요타는 통합형 제품에 강하다. 전기차가 모듈형 제품에 가깝다면 하이브리드 차량은 통합형 제품에 가깝다. 일본의 전자 메이커가 무너진 이유는 전자 제품이 모듈화되었기 때문이다. 따라서 제품 관점에서 전기차로의 전환은 토요타에 최대의 위기일 수 있다.
“구조는 전략을 따른다”
공장을 운영하고 만드는 철학에서도 크게 두 가지 관점이 존재한다. 가능하면 인력을 배제하고 자동화를 많이 하고 싶어 하는 기업이 있다. 이런 기업은 고급 기술자와 현장 작업자를 구분하고, 로봇이 작업을 해야 더 높은 품질을 확보할 수 있다고 믿는다. 지금 테슬라의 언박스드 프로세스는 자동화 기계와 로봇으로 차를 만들고 싶은데 차량 구조로 인해 불가능하자, 차량의 구조와 조립 방법 전체를 변경해 자동화하겠다는 의지의 결과물이다. 한편 강한 노조(勞組)가 있는 회사도 보통 공장 자동화에 집착한다. 현대자동차와 닛산이 그 예이다.
반대로 자동화도 좋지만, 작업자의 역할을 중시하는 회사도 있다. 토요타가 대표적이다. 엔지니어와 공장 작업자 간의 구분을 좋아하지 않는다. 그래서 토요타는 본사 직원도 작업복을 입고, 사장도 곧잘 작업복 차림으로 사내 행사에 참가한다.
이처럼, 자동차 메이커에 따라 제품에 대한 철학, 공장에 대한 철학은 서로 다르다.
미국의 유명한 경영 사상가 알프레드 챈들러(1918~2007년)는 “구조는 전략을 따른다(Structure follows strategy)”라는 말을 남겼다. 조직이 추구하는 전략에 따라 이를 뒷받침하는 조직의 구조가 달라진다는 의미이다. 지금 전기차 공장이 그렇다. 기업별로 전기차에 대한 나름의 전략이 서 있을 것이다. 단, 외부에서는 정확히 알기 힘들다. 하지만 공장을 보면 어떤 전략으로 움직이고 있는지 추정할 수 있다.
테슬라 의식하는 토요타

일정 정도 규모가 되는 회사는 전기차 전용 공장을 만들기도 하고, 또 기존 내연(內燃)기관, 하이브리드 자동차와 같은 생산 라인에서 만들기도 한다. 혼류 생산(混流生産·Mixed Production)은 하나의 생산 라인에서 여러 동력원의 차를 만드는 것을 의미한다.
닛산의 도치기(栃木) 공장이 혼류 생산 라인의 대표적인 공장이다. 2021년 10월 닛산은 기존 공장을 완전히 리뉴얼하여 ‘닛산 인텔리전트 팩토리(NIF)’라는 콘셉트의 공장을 선보였다. 약 5400명이 근무하는 도치기 공장은 연 30만 대를 생산할 수 있는 공장으로 전기차 ‘아리스’ 외에 시마 하이브리드, 인피니티 브랜드의 차량을 생산한다. 다양한 동력원을 가지는 차량을 하나의 공장에서 만들기 위해 ‘SUMO’라는 ‘파워트레인 일괄 탑재 시스템’을 만들었다. 이것은 프런트, 센터, ‘리어’로 분할한 2층 구조의 팔레트를 사용하는 방식이다.(〈그림5〉 참조)
토요타의 전기차 공장에 대한 모습은 아직 잘 알려져 있지 않다. 하지만 새롭게 사장에 취임한 사토 고지(佐藤恒治·54)는 4월 7일 신경영체제 발표회에서 전기차 공장의 공정 수를 2분의 1로 줄이고, 생산, 연구개발, 비즈니스를 한 명의 리더 밑에서 운영하는 ‘BEV 팩토리’ 라는 조직을 만들 것이라고 발표했다. 다분히 테슬라를 의식한 발언이다.
보통 제품의 혁신이 일어나고 어느 정도 제품의 형태가 고정되면 공장의 혁신이 일어나기 마련이다. 기존 내연기관 대비 심플한 형태의 전기차가 좀 더 대중화되기 위해 공장 영역에서 다양한 혁신이 생길 수 있다. 테슬라가 먼저 시작했다. 아마 다른 모든 자동차 메이커는 촉각을 곤두세우고 있을 듯하다.
생산성에 대한 잘못된 생각
자동차 산업의 전환기가 본격화되고 있다. 이제 제품으로서의 전기차는 당연한 것으로 받아들여지고 있다. 이제 혁신의 방향이 공장 부문으로까지 전개되고 있다. 이에 한국 제조 기업이 공장(생산) 관점에서 반성해야 할 점, 고쳐야 할 점에 대한 논의가 필요하다. 필자가 생각하는 몇 가지 이슈는 다음과 같다.
첫째, 한국 사회 전체가 공장에 대한 이해 수준을 올려야 한다. 공장에 대한 잘못된 신문기사를 보면 우리가 공장을 얼마나 왜곡되게 이해하는지 알 수 있다. 그 대표적인 사례가 ‘시간당 생산 대수(Units Per Hour·UPH)가 생산성’이라는 잘못된 믿음이다. 가령 ‘울산 공장의 시간당 차량 생산 대수는 평균 45대로, 미국 앨라배마 공장(68대)의 3분의 2 수준에 불과하다. 그래서 생산성이 떨어진다’라는 논조의 기사가 매년 주기적으로 보도된다. 하지만 컨베이어 속도를 지칭하는 UPH는 생산성과 비례하지 않는다.
생산성이란 입력 대비 출력이다. 여기서 입력(Input)은 생산하기 위해 투입한 요소로, 사람이 컨트롤할 수 있는 인자(因子)여야 한다. 노동력이 대표적이다. 그리고 출력(Output)은 경제적으로 유용한 산출물을 의미한다. 즉 생산성을 올린다는 것은 기업이 어떤 의도를 가지고 노력하여 동일한 입력으로 보다 많은 산출물을 만들어내거나 동일한 산출량을 보다 적은 입력으로 만들어내는 것을 의미한다.
예를 들어 A공장은 100명의 근로자가 10시간 일해서 500대의 차량을 만든다. B공장의 경우 200명의 근로자가 10시간 일해서 700대의 차량을 생산한다. B공장의 UPH는 70(=700대/10시간)으로 A공장의 UPH 50(=500대/10시간)보다 높다. 하지만 노동생산성은 A공장이 0.5(=500대/(100명×10시간))이고, B공장은 0.35(=700대/(200명×10시간))로 A공장이 높다. 즉 B공장은 A공장보다 UPH가 높지만, 노동생산성은 떨어진다. 간단한 산수임에도 불구하고 10여 년 이상 한국의 신문은 지속적으로 잘못된 보도를 반복했다. ‘뭐든지 빨라야 한다’는 잠재의식이 작용해서인지 컨베이어 벨트가 빨라야 노동생산성을 올릴 수 있다는 오해가 뿌리 깊게 자리 잡고 있다. 보통 제품의 크기, 작업자의 숙련도 등에 따라 적절한 컨베이어 벨트 속도(UPH)가 존재한다.
공장이 변해야 한다
둘째, 한국 제조 기업의 현장, 즉 공장은 한 가지 방식으로 설명하기 곤란하다. 국내의 A기업은 전 세계 최하위의 생산성을 보이는 반면, 또 다른 업종의 B기업은 전 세계 최상위의 생산성을 자랑한다. 가령 창원에 있는 볼보코리아는 볼보그룹에서 평가하는 글로벌 생산성 평가에서 최고 성적을 보이고 있고, 안산에 있는 캐논코리아 또한 일본의 캐논 공장보다 더 높은 생산성을 보인다. 심지어 캐논코리아의 생산본부장은 정년 퇴임 후 일본의 어떤 기업에 스카우트되어 공장 생산성을 3배로 올리는 역할을 했다. 한국 공장의 생산성은 업종별·기업별로 편차가 심하다.
셋째, 생산성이 낮은 공장을 보면 보통 공장과 연구소, 본사 간에 높은 벽이 있다. 그래서 연구소, 본사 인원이 좀처럼 공장에 가지 않는다. 현장에 강한 노조가 있기 때문일 수도 있다. 하지만 보통 노조가 강한 회사일수록 본사도 강한 경우가 많다. 회사는 유기체와 같아서 각 부문 간에 그리고 구성원 간에는 서로 닮아가기 마련이다. 차라리, 현장은 거울 속에 비친 본사의 또 다른 모습이라 이해하는 것이 좋다.
이런 조직은 본사와 현장 간의 높은 벽으로 인해 본사에 현장을, 공장을 제대로 볼 수 있는 사람이 부족하다. 그저 규모가 크고 자동화 설비가 잘 갖춰져 있으면 좋은 공장이라고 착각한다.
또 국내 공장은 생산성이 떨어지지만 해외 공장은 다르다고 생각한다. 그러나 해외 공장 또한 국내 공장의 연장선상에 있다고 봐야 한다. 중국의 토요타 공장은 일본의 토요타 공장과 닮았고, 중국의 아우디 공장은 독일의 아우디 공장과 닮았다. 운영 방식까지 비슷하다. 중국에 있는 공장이라고 중국 토요타 공장과 중국 아우디 공장이 비슷한 것은 아니다. 결국 외국 공장을 잘 운영하려면 국내 공장을 잘 운영해야 한다.
지금은 자동차 산업의 대전환기다. 어떤 형태로든 공장의 변신이 필수적이다. 이럴 때일수록 제조 기업의 경영층, 엔지니어, 현장 근로자는 능동적으로 변화에 대응할 필요가 있다. 지금 가장 절실한 것은 미래의 공장에 대한 이미지를 떠올릴 수 있어야 한다는 것이다. 전기차만 만드는 테슬라는 변화된 미래 전기차 공장의 모습을 떠올리고 언박스드 프로세스라는 용어를 만들어서 제시하고 있다. 아마 일론 머스크가 공장의 야전침대에서 숙식을 해결하면서 생산 문제를 직접 몸으로 체험했기 때문에 가능했을 것이다.
전기자동차 시대, 한국 공장의 철저한 변신이 요구된다. 그 변신은 공장에 직접 가서 보고 행동하는 것에서부터 출발한다.⊙
CASE라는 키워드를 곰곰이 살펴보면 기존 자동차 산업을 부정하는 용어로 이해된다. 즉 독립공간인 차에 연결성을 부여하고, 운전의 즐거움을 강조하는 기존 차량과 달리 자율주행을 추구하고, 또 차량을 소유하지 않고 공유하며, 엔진이 아닌 배터리와 모터로 움직이는 자동차를 의미하기 때문이다. 많은 메이커들은 이처럼 지난 100년간의 자동차 산업의 역사를 부정하고 있다.
테슬라의 언박스드 프로세스
테슬라는 3월 1일 인베스터데이(Investor day)에서 또다시 자동차 생산 방식에 대해 부정했다. 언박스드 프로세스(Unboxed Process)가 바로 그것이다. 지금까지 자동차 메이커는 차량의 골격에 해당하는 차체(Body)를 먼저 완성시키고 난 뒤에 차체에 부품을 하나씩 장착하면서 차량을 완성했다. 하지만 테슬라는 차량을 6개의 빅 모듈(Big Module)의 조립만으로 완성하겠다고 발표했다. 이 방법을 통해 전기차의 제조 코스트를 2분의 1로 줄이겠다고까지 했다.
물론 이것을 실현하기 위해서는 해결해야 할 기술적 난제가 많을 것이다. 하지만 일론 머스크와 테슬라가 생각하는 자동차의 설계와 생산 철학을 살펴볼 필요는 있다. 테슬라의 이번 발표를 그냥 넘기기에는 제조업이 생산시스템에서 차지하는 비중이 크기 때문이다. 생산은 개발과 함께 제조업을 이루는 양대 축에 해당한다. 현대자동차의 경우, 경기도 화성의 남양연구소에서 차량을 개발하고, 울산 공장에서 차량을 생산한다. 물론 서울 양재동의 본사에서도 다양한 업무를 처리하지만, 제조업의 본질, 그리고 현대자동차를 구성하는 인력의 분포를 보더라도 연구소와 공장을 2개의 축으로 볼 수 있다.
테슬라는 사물을 제로 상태에서 바라보면서 근본적인 문제 해결을 추구하는 기업이다. 그동안 테슬라의 일론 머스크는 기존 자동차 생산시스템에 대한 지속적인 의문을 제기해왔다. 이번 기회를 통해 제조업에서 생산시스템의 주요 이슈와 변화 방향에 대해 살펴볼 필요가 있다.
먼저 테슬라가 발표한 언박스드 프로세스가 무엇인지 설명하겠다. 그리고 기존 메이커가 개선해온 생산 방식의 특징과 전기차를 생산하는 방식에 대해 살펴보고, 한국 제조 기업이 처한 상황과 나아가야 할 방향에 대해 논의하는 기회를 가지려고 한다.
기존 자동차 제작 공정
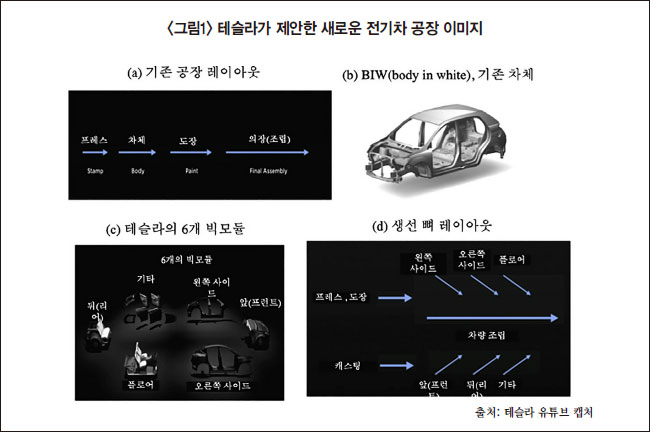
먼저 기존 자동차 공장의 생산 방식을 살펴보자. 기존 자동차 공장은 프레스, 차체, 도장, 의장(조립) 공장의 순서로 구성되어 있다.
연구소에서 제품을 설계하면 설계 정보를 금형(金型)이란 큰 틀에 새겨 넣는다. 그리고 금형을 프레스 기계에 상하로 장착하고 철판을 금형 사이에 두고 세게 누른다. 그러면 철판은 설계된 형상으로 변형된다. 이후 성형(成型)된 부품을 차체 공장에서 용접하여 3차원 형상의 차체를 만든다. 자동차 회사에서는 이것을 BIW(Body in White) 또는 화이트 보디(White body)라고 한다. 아직 페인팅이 되기 전의 상태이기에 붙여진 이름이다. 차량의 골격을 정확하게 용접하지 않으면 내구 성능, 충돌 성능 등이 나빠지기에 상당히 주의를 기울인다.
이후 이 BIW를 도장공장에서 페인팅하고, 의장(조립) 공장에서 도어를 제거한 뒤에 차량 내부에 부품을 장착한다. 그러고 차량 하부에 차의 기본 성능을 좌우하는 섀시(chassis) 부품(예를 들면, 엔진, 서스펜션 등)을 장착한다. 마지막으로 도어를 다시 장착하여 차량을 완성한다. 물론, 프레스, 차체, 도장, 의장 공장 사이에 재고(在庫) 창고가 있지만, 하나의 선(라인)이 순차적으로 연결된 형태라고 생각해도 큰 무리가 없다.(〈그림1〉 (a), (b) 참조)
언박스드 프로세스, 자동화 용이
기존 자동차 메이커는 BIW(또는 화이트 보디)라는 차체의 형상을 먼저 만들고 난 뒤에 차량 내부의 부품을 조립한다. 이 경우 차량 내부에 조립 설비가 들어가고 나오기가 어려워 일정 비율 이상 자동화가 어렵다. 그래서 어쩔 수 없이 사람이 계속 차 밖에서 부품을 잡아 차 안으로 들어가서 부품을 조립한다. 당연히 생산성이 떨어진다.
테슬라의 새로운 공정은 3차원 폐공간(closed space), 즉 BIW를 만들지 않겠다는 발상에서 출발한다. 테슬라는 차량을 크게 6개 모듈(차량 앞, 중간, 뒤 부분과 왼쪽·오른쪽 사이드, 기타 부분)로 나누어서 페인팅과 조립을 완료하고 난 뒤에 마지막 단계에서 6개의 빅 모듈을 하나로 합쳐 한 대의 차를 만들고자 한다. 그리고 자동차 공장의 레이아웃(layout)도 기존의 1자 라인에서 생선뼈와 같은 형태의 레이아웃으로 완전히 변화시킬 에정이다.(〈그림1〉 (c), (d) 참조)
직선으로 연결된 기존 자동차 공장의 레이아웃과 테슬라가 제안한 생선뼈 모양의 레이아웃 간의 차이를 살펴보자.
언박스드 프로세스의 장점은 첫째, 자동화에 의한 생산성 향상이다. 앞서 말한 것처럼 BIW는 박스(box) 형태의 폐공간 때문에 자동화가 힘들다. 현재 의장 공장의 자동화율은 15% 수준으로 알려져 있다. 하지만 테슬라의 언박스드 프로세스는 오픈된 공간에서 모듈 단위로 조립하기 때문에 자동화가 용이하다. 그리고 작업자의 접근성이 높아져 생산성을 올릴 수 있다.

둘째, 차량을 제작하는 데 소요되는 시간(리드타임)을 극적으로 단축시킬 수 있다. 기존 공장은 4개의 공장을 직렬로 배치하여 공정이 순차적으로 진행되기 때문에 일정 정도 시간이 걸린다. 하지만 언박스드 프로세스는 6개의 빅 모듈이 동시 병행으로 조립하기 때문에 한 대의 차를 제작하는 데 소요되는 시간(리드타임)을 극적으로 단축시킬 수 있다.(〈그림2〉 참조)
셋째, 공장을 콤팩트화할 수 있다. ‘생선뼈’처럼 생긴 레이아웃은 척추(backbone)에 해당하는 메인 라인과 6개의 서브 라인으로 구성되어 있다. 이것은 현재 생산 라인보다 훨씬 더 콤팩트한 생산 라인을 만들 수 있다. 테슬라는 생산 라인의 설치 면적을 40% 이상 줄일 수 있다고 한다. 생산 라인의 소형화는 공장을 신·증설할 때 위력을 발휘한다. 기존 생산 방식보다 초기 투자 비용을 절감할 수 있을 뿐 아니라 공사 기간도 줄일 수 있다. 즉 보다 저렴한 비용으로 빠르게 전기차 양산 공장을 만들 수 있다.
테슬라는 언박스드 프로세스를 도입하여 대폭적인 비용 절감을 노리고 있다. 현재 고객은 테슬라가 만들고 있는 ‘모델3’의 절반 가격(2만5000달러)인 전기차를 기대하고 있다. 테슬라는 2030년에 2000만 대의 차량을 생산하겠다고 발표한 적이 있다. 이 목표를 달성하기 위해서는 대중적인 가격의 차가 필수적이며 언박스드 프로세스가 해결안이 될 수 있다. 6개 빅 모듈의 조립만으로 하나의 차량을 만들기 위해서는 차량 설계를 근본부터 다시 변경해야 한다. 그래서 테슬라는 설계와 생산 기술 부문이 서로 같은 팀에서 일하고 있다. 아마도 언박스드 프로세스에 가장 적합한 형태로 차량을 새롭게 개발할 것이다.
테슬라, 공장 개념의 전환
여기서 관심 있게 보아야 할 것이 하나 더 있다. 테슬라는 그동안 전개해온 ‘기가 팩토리(giga factory)’라는 공장 개념을 가지고 있었다. 그런데 갑자기 언박스드 프로세스라는 것을 들고나왔다는 점이다.
기가 팩토리는 테슬라가 GM과 토요타로부터 인수한 캘리포니아의 프리몬트(Fremont) 공장에 이어 본격적으로 생산량 확대를 위해 만든 표준 공장에 대한 개념이다. 중국 상하이(2019년 10월), 독일 베를린(2022년 3월)에 이어 미국 텍사스(2022년 4월)에서도 가동을 시작했다. 테슬라는 자사 공장에 ‘기가(giga)’라는 이름을 붙일 만큼 공장 규모가 크다는 것을 자랑했다. 텍사스 공장의 길이는 1166m로, 현존하는 세계 최고 높이의 건축물인 163층의 부르즈 할리파 빌딩의 높이 829m보다 길다. 면적은 약 40만㎡에 달한다. 이것은 100년 전 헨리 포드가 만든 공장과 닮았다.
사실, 테슬라의 거대한 공장 규모는 자동차 메이커가 글로벌 톱 메이커로 올라서는 과정에서 거쳐 간 과정과 유사하다. 헨리 포드가 1928년에 완공한 리버루즈 공장은 자동차 공장 내에 제철소까지 만들었다. 일본의 토요타가 1950년대 말, 1960년대 중반에 건설한 모토마치 공장과 다카오카 공장 또한 당시에는 나름 거대한 공장이었다. VW(폴크스바겐)의 볼프스부르크 공장과 현대자동차의 울산 공장 또한 세계적인 규모의 공장이다. 현대자동차는 울산 공장 내에 5개의 완성차 공장과 함께, 엔진 공장, 변속기 공장과 수출 항구까지 갖추고 있다.
그런데 2023년 테슬라는 자신이 만든 ‘기가 팩토리’라는 공장 콘셉트를 바꾸고자 한다. 어쩌면 테슬라의 장점은 바로 이렇게 스스로 변신할 수 있다는 점일 것이다.

테슬라가 언박스드 프로세스를 통해 공장을 콤팩트화하고 생산리드타임을 줄이겠다고 하지만, 사실 이것은 토요타 생산 방식의 핵심이다. 여기서 토요타 자동차 공장을 어떻게 개선해왔는지를 살펴보자.
토요타는 고객의 변화에 유연하게 대응할 수 있는 공장을 만들기를 원한다. 코스트 저감보다 업무 프로세스 개선이 더 중요하며 공장에서의 생산 흐름을 개선하면 자연스럽게 코스트는 저감될 것이라고 생각한다. 그래서 토요타가 제시한 공장 콘셉트는 심플(Simple), 슬림(Slim), 콤팩트(Compact)다. 줄여서 SSC라고 표현한다. 가능한 한 적은 투자비로 고정비를 줄이고 공장을 콤팩트하게 만들어 공장의 운영 비용을 줄이고자 한다. 좁은 공간에 로봇을 많이 설치하고, 노동 생산성을 올려 작업자의 수를 축소한다.
〈그림3〉(a)는 토요타 그룹의 경차 전문 메이커인 다이하츠가 이루어낸 성과물을 수치로 나타낸 것이다. 2004년 11월에 다이하츠는 규슈의 나카츠에 400억 엔을 투자하여 23만 대 규모의 공장을 건설하였다. 종업원 수는 약 2100명으로 경차와 소형차를 만든다. 이후 SSC 개념으로 공장을 혁신했다. 즉 2007년 11월에 만들어진 나카츠 제2공장은 235억 엔을 투자하여 제1공장의 절반의 면적에 동일한 생산 능력을 가지게 되었다. 종업원 수는 약 400명으로 제1공장의 19% 수준에 불과하다. 〈그림3〉(b)는 다이하츠의 나카츠 공장을 인공위성에서 찍은 사진이다. 왼쪽에 있는 나카츠 제1공장과 비교해 오른쪽의 제2공장이 동일한 생산 능력을 갖추고 있음에도 불구하고 얼마나 콤팩트하게 만들어졌는지 알 수가 있다.
생선뼈 형태의 공장 레이아웃
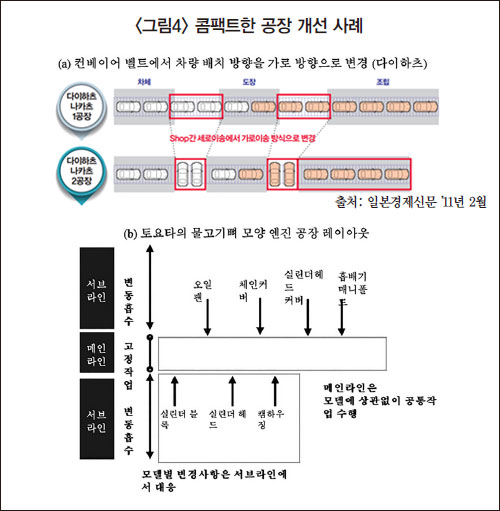
나카츠 제2공장에서 투자비를 줄인 예를 살펴보자. 먼저 차체를 용접하는 데 필요한 지그(Jig)를 없앴다. 보통 차체를 용접할 때에 차종마다 전용으로 설계한 지그가 용접하는 철판을 잡아준다. 하지만 많은 비용이 드는 지그 대신 로봇이 용접할 위치를 잡아 고정시킨 후에 용접한다. 이렇게 하여 지그 설치 비용을 줄였으며, 다양한 차종의 용접을 큰 비용의 증가 없이 용접할 수 있었다.
한편, 차체-도장-조립 공장 간 이송할 때 차량을 컨베이어 벨트상에 세로 방향으로 돌려서 이송하여 컨베이어 벨트 길이를 줄였다.(〈그림4〉(a) 참조) 이 외에 좁은 공간에 많은 로봇을 설치하였다. 나카츠 제1공장이 단위면적당 3.8대의 로봇이 설치되어 있는데, 나카츠 제2공장은 단위면적당 로봇이 11.4대가 설치되어 약 3배 정도로 로봇 설치 밀도를 올렸다.
그리고 테슬라가 언박스드 프로세스에서 발표한 생선뼈 형태의 공장 레이아웃도 사실 처음은 아니다. 〈그림4〉(b)는 토요타가 10년 전에 만든 엔진 공장의 레이아웃이다. 하나의 엔진 생산 라인에서 다양한 종류의 엔진을 만들기 위해 고안된 방식으로 엔진에 장착되는 각종 부품의 생산을 서브 라인으로 만들어두었다.
물론, 완성차 조립에 이런 레이아웃을 적용하겠다고 시도하는 것은 분명 테슬라가 처음이다. 테슬라와 토요타가 같이 생선뼈와 같은 레이아웃에 도달했지만, 공장을 통해 추구하는 목표는 서로 다르다. 테슬라는 철저하게 공장 자동화를 하고 싶어 하고, 토요타는 동일한 생산 라인에서 다양한 제품을 만들고 싶어 한다.
모듈형 vs 통합형
자동차 메이커는 저마다 창업 이후 성장하는 과정 속에서 시련을 겪고 또 문제를 해결해나갔다. 그러면서 그 경험이 조직의 노하우로 정착되었다. 결국 조직이 가지고 있는 경험이 지금과 같은 자동차 산업의 전환기에 서로 다른 의사 결정을 만들어낸다는 말이다. 또 제품과 일하는 방식에도 반영된다.
이런 의미에서 미국 실리콘 밸리에서 탄생한 테슬라는 확실히 모듈 관점이 강하다. 모듈이란 부품의 사이즈와 용도가 표준화되어 서로 교체하기 쉬운 설계 방식을 의미한다. 마치 레고처럼 인터페이스가 표준화된 부품으로 전체 제품을 만들겠다는 발상이다. 가령, 테슬라가 전기차에 사용한 배터리를 살펴보자. 테슬라는 18650 원통형 배터리(직경 28mm, 길이 65mm)를 사용하는데 이것은 과거 비디오 카메라용 배터리로 개발된 것이다. 테슬라는 18650 원통형 배터리 약 7000개를 서로 연결하여 전기차용 배터리로 사용한다. 모듈적인 제품 개발 방식이다. 테슬라가 새롭게 제안하는 자동차 조립 기술인 언박스드 프로세스는 차를 6개의 빅모듈의 조합으로 만든다는 것으로 모듈 생산의 끝판왕이라 할 수 있다.
이와 반대되는 설계 철학을 가지고 있는 회사가 있다. 바로 토요타이다. 토요타는 차량에 맞는 배터리가 필요하다고 생각한다. 이렇게 제품에 특화(特化)된 부품으로 개발된 제품을 통합형(Integrated) 제품이라고 한다. 일본의 제조 기업, 특히 토요타는 통합형 제품에 강하다. 전기차가 모듈형 제품에 가깝다면 하이브리드 차량은 통합형 제품에 가깝다. 일본의 전자 메이커가 무너진 이유는 전자 제품이 모듈화되었기 때문이다. 따라서 제품 관점에서 전기차로의 전환은 토요타에 최대의 위기일 수 있다.
“구조는 전략을 따른다”
공장을 운영하고 만드는 철학에서도 크게 두 가지 관점이 존재한다. 가능하면 인력을 배제하고 자동화를 많이 하고 싶어 하는 기업이 있다. 이런 기업은 고급 기술자와 현장 작업자를 구분하고, 로봇이 작업을 해야 더 높은 품질을 확보할 수 있다고 믿는다. 지금 테슬라의 언박스드 프로세스는 자동화 기계와 로봇으로 차를 만들고 싶은데 차량 구조로 인해 불가능하자, 차량의 구조와 조립 방법 전체를 변경해 자동화하겠다는 의지의 결과물이다. 한편 강한 노조(勞組)가 있는 회사도 보통 공장 자동화에 집착한다. 현대자동차와 닛산이 그 예이다.
반대로 자동화도 좋지만, 작업자의 역할을 중시하는 회사도 있다. 토요타가 대표적이다. 엔지니어와 공장 작업자 간의 구분을 좋아하지 않는다. 그래서 토요타는 본사 직원도 작업복을 입고, 사장도 곧잘 작업복 차림으로 사내 행사에 참가한다.
이처럼, 자동차 메이커에 따라 제품에 대한 철학, 공장에 대한 철학은 서로 다르다.
미국의 유명한 경영 사상가 알프레드 챈들러(1918~2007년)는 “구조는 전략을 따른다(Structure follows strategy)”라는 말을 남겼다. 조직이 추구하는 전략에 따라 이를 뒷받침하는 조직의 구조가 달라진다는 의미이다. 지금 전기차 공장이 그렇다. 기업별로 전기차에 대한 나름의 전략이 서 있을 것이다. 단, 외부에서는 정확히 알기 힘들다. 하지만 공장을 보면 어떤 전략으로 움직이고 있는지 추정할 수 있다.
테슬라 의식하는 토요타

일정 정도 규모가 되는 회사는 전기차 전용 공장을 만들기도 하고, 또 기존 내연(內燃)기관, 하이브리드 자동차와 같은 생산 라인에서 만들기도 한다. 혼류 생산(混流生産·Mixed Production)은 하나의 생산 라인에서 여러 동력원의 차를 만드는 것을 의미한다.
닛산의 도치기(栃木) 공장이 혼류 생산 라인의 대표적인 공장이다. 2021년 10월 닛산은 기존 공장을 완전히 리뉴얼하여 ‘닛산 인텔리전트 팩토리(NIF)’라는 콘셉트의 공장을 선보였다. 약 5400명이 근무하는 도치기 공장은 연 30만 대를 생산할 수 있는 공장으로 전기차 ‘아리스’ 외에 시마 하이브리드, 인피니티 브랜드의 차량을 생산한다. 다양한 동력원을 가지는 차량을 하나의 공장에서 만들기 위해 ‘SUMO’라는 ‘파워트레인 일괄 탑재 시스템’을 만들었다. 이것은 프런트, 센터, ‘리어’로 분할한 2층 구조의 팔레트를 사용하는 방식이다.(〈그림5〉 참조)
![]() |
사토 고지 신임 토요타 사장이 렉서스 수석 엔지니어였던 2016년 렉서스 스포츠 하이브리드차 LC500h를 직접 모는 모습. 사진=렉서스 |
보통 제품의 혁신이 일어나고 어느 정도 제품의 형태가 고정되면 공장의 혁신이 일어나기 마련이다. 기존 내연기관 대비 심플한 형태의 전기차가 좀 더 대중화되기 위해 공장 영역에서 다양한 혁신이 생길 수 있다. 테슬라가 먼저 시작했다. 아마 다른 모든 자동차 메이커는 촉각을 곤두세우고 있을 듯하다.
생산성에 대한 잘못된 생각
자동차 산업의 전환기가 본격화되고 있다. 이제 제품으로서의 전기차는 당연한 것으로 받아들여지고 있다. 이제 혁신의 방향이 공장 부문으로까지 전개되고 있다. 이에 한국 제조 기업이 공장(생산) 관점에서 반성해야 할 점, 고쳐야 할 점에 대한 논의가 필요하다. 필자가 생각하는 몇 가지 이슈는 다음과 같다.
첫째, 한국 사회 전체가 공장에 대한 이해 수준을 올려야 한다. 공장에 대한 잘못된 신문기사를 보면 우리가 공장을 얼마나 왜곡되게 이해하는지 알 수 있다. 그 대표적인 사례가 ‘시간당 생산 대수(Units Per Hour·UPH)가 생산성’이라는 잘못된 믿음이다. 가령 ‘울산 공장의 시간당 차량 생산 대수는 평균 45대로, 미국 앨라배마 공장(68대)의 3분의 2 수준에 불과하다. 그래서 생산성이 떨어진다’라는 논조의 기사가 매년 주기적으로 보도된다. 하지만 컨베이어 속도를 지칭하는 UPH는 생산성과 비례하지 않는다.
생산성이란 입력 대비 출력이다. 여기서 입력(Input)은 생산하기 위해 투입한 요소로, 사람이 컨트롤할 수 있는 인자(因子)여야 한다. 노동력이 대표적이다. 그리고 출력(Output)은 경제적으로 유용한 산출물을 의미한다. 즉 생산성을 올린다는 것은 기업이 어떤 의도를 가지고 노력하여 동일한 입력으로 보다 많은 산출물을 만들어내거나 동일한 산출량을 보다 적은 입력으로 만들어내는 것을 의미한다.
예를 들어 A공장은 100명의 근로자가 10시간 일해서 500대의 차량을 만든다. B공장의 경우 200명의 근로자가 10시간 일해서 700대의 차량을 생산한다. B공장의 UPH는 70(=700대/10시간)으로 A공장의 UPH 50(=500대/10시간)보다 높다. 하지만 노동생산성은 A공장이 0.5(=500대/(100명×10시간))이고, B공장은 0.35(=700대/(200명×10시간))로 A공장이 높다. 즉 B공장은 A공장보다 UPH가 높지만, 노동생산성은 떨어진다. 간단한 산수임에도 불구하고 10여 년 이상 한국의 신문은 지속적으로 잘못된 보도를 반복했다. ‘뭐든지 빨라야 한다’는 잠재의식이 작용해서인지 컨베이어 벨트가 빨라야 노동생산성을 올릴 수 있다는 오해가 뿌리 깊게 자리 잡고 있다. 보통 제품의 크기, 작업자의 숙련도 등에 따라 적절한 컨베이어 벨트 속도(UPH)가 존재한다.
공장이 변해야 한다
![]() |
현대차가 지난해 출시한 전기차 아이오닉 5(왼쪽 앞)가 내연기관차 코나(오른쪽)와 함께 울산 공장에서 생산되고 있다. 2025년 전기차 전용 공장이 완공되면 현대차의 전기차 생산 체계는 완전히 재편될 것으로 전망된다. 사진=현대자동차 |
셋째, 생산성이 낮은 공장을 보면 보통 공장과 연구소, 본사 간에 높은 벽이 있다. 그래서 연구소, 본사 인원이 좀처럼 공장에 가지 않는다. 현장에 강한 노조가 있기 때문일 수도 있다. 하지만 보통 노조가 강한 회사일수록 본사도 강한 경우가 많다. 회사는 유기체와 같아서 각 부문 간에 그리고 구성원 간에는 서로 닮아가기 마련이다. 차라리, 현장은 거울 속에 비친 본사의 또 다른 모습이라 이해하는 것이 좋다.
이런 조직은 본사와 현장 간의 높은 벽으로 인해 본사에 현장을, 공장을 제대로 볼 수 있는 사람이 부족하다. 그저 규모가 크고 자동화 설비가 잘 갖춰져 있으면 좋은 공장이라고 착각한다.
또 국내 공장은 생산성이 떨어지지만 해외 공장은 다르다고 생각한다. 그러나 해외 공장 또한 국내 공장의 연장선상에 있다고 봐야 한다. 중국의 토요타 공장은 일본의 토요타 공장과 닮았고, 중국의 아우디 공장은 독일의 아우디 공장과 닮았다. 운영 방식까지 비슷하다. 중국에 있는 공장이라고 중국 토요타 공장과 중국 아우디 공장이 비슷한 것은 아니다. 결국 외국 공장을 잘 운영하려면 국내 공장을 잘 운영해야 한다.
지금은 자동차 산업의 대전환기다. 어떤 형태로든 공장의 변신이 필수적이다. 이럴 때일수록 제조 기업의 경영층, 엔지니어, 현장 근로자는 능동적으로 변화에 대응할 필요가 있다. 지금 가장 절실한 것은 미래의 공장에 대한 이미지를 떠올릴 수 있어야 한다는 것이다. 전기차만 만드는 테슬라는 변화된 미래 전기차 공장의 모습을 떠올리고 언박스드 프로세스라는 용어를 만들어서 제시하고 있다. 아마 일론 머스크가 공장의 야전침대에서 숙식을 해결하면서 생산 문제를 직접 몸으로 체험했기 때문에 가능했을 것이다.
전기자동차 시대, 한국 공장의 철저한 변신이 요구된다. 그 변신은 공장에 직접 가서 보고 행동하는 것에서부터 출발한다.⊙